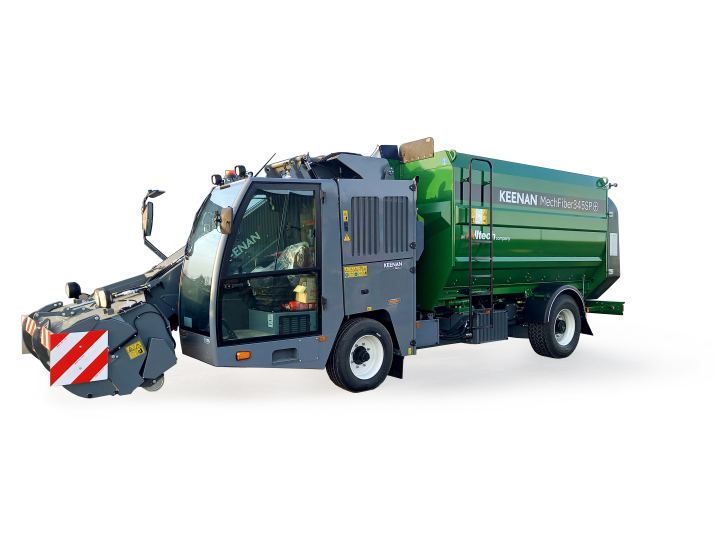
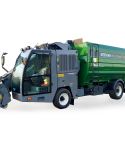

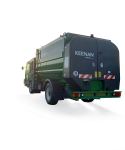
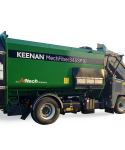
Category: Self-Propelled
Size:Height : 3,040mm (120")
Width : 2,550mm (100.5")
Horsepower : 170 HP
Dairy Cows per load : 65-100
Finishers per load : 130-200
KEENAN MechFiber345SP+ features
- Consistently delivering the patented KEENAN MechFiber mix, with a capacity of 16 cubic metres
- Heavy duty sealed oil-bath drive system
- Exclusive Storti mechanical transmission, reducing fuel consumption by up to 25 percent
- Cutter head designed and tested to ensure protection of forage structure for optimum mix quality
- Ultimate in operator comfort and control with twin video cameras and in-cab monitor for visibility, climate control (optional) and pneumatic seat
- Reduced noise and running costs
- Left and right front discharge via adjustable conveyor for homogeneous distribution of total mixed ration (TMR)
- Available with the KEENAN controller, providing the optimum in TMR management and feed efficiency
Class-leading cutter head technology
The cutter head on the KEENAN MechFiber345SP+ has been engineered to deliver rapid loading of a vast number of products (grass silage, hay, waxy maize, pulp, pellets, flour, square or round bales of straw or hay, etc.) leaving a clean, uniform face for optimum clamp management.
The tungsten-coated blades feature a unique crossed arrangement, performing clean cuts without damaging the structure of the fibre, even with very compact silages.
Speed. Precision. Versatility.
The unique placement of the blades and configuration of the loading channel allows the cutter head to load in both directions, and easily run in reverse if needed. The high speed loading belt delivers a significantly reduced mix preparation time.
Design & ease of maintenance
Features mechanical drive to the six-paddle reel. This exclusive engineering system, by means of a specially designed gearbox and PTO shaft, transfers all the power from the engine to the mixing system, thus reducing fuel consumption (by up to 25 percent) as well as reducing maintenance costs.
Since there is no hydraulic pump and motor, the risk of expensive replacements and/or downtime is reduced. The drive to the mixer paddle is performed by means of a specially designed hydraulic clutch activated by an electric button situated in the cabin. The operator is free to start and stop the mixing system at any time.